Abstract
Airborne wind energy (AWE) vehicles maximize energy production by constantly operating at extreme wing loading, permitted by high flight speeds. Additionally, the wide range of wind speeds and the presence of flow inhomogeneities and gusts create a complex and demanding flight environment for AWE systems. Adaptation to different flow conditions is normally achieved by conventional wing control surfaces and, in case of ground generator-based systems, by varying the reel-out speed. These control degrees of freedom enable to remain within the operational envelope, but cause significant penalties in terms of energy output. A significantly greater adaptability is offered by shape-morphing wings, which have the potential to achieve optimal performance at different flight conditions by tailoring their airfoil shape and lift distribution at different levels along the wingspan. Hence, the application of compliant structures for AWE wings is very promising. Furthermore, active gust load alleviation can be achieved through morphing, which leads to a lower weight and an expanded flight envelope, thus increasing the power production of the AWE system. This work presents a procedure to concurrently optimize the aerodynamic shape, compliant structure, and composite layup of a morphing wing for AWE applications. The morphing concept is based on distributed compliance ribs, actuated by electromechanical linear actuators, guiding the deformation of the flexible—yet load-carrying—composite skin. The goal of the aerostructural optimization is formulated as a high-level requirement, namely to maximize the average annual power production per wing area of an AWE system by tailoring the shape of the wing, and to extend the flight envelope of the wing by actively alleviating gust loads. The results of the concurrent multidisciplinary optimization show a 50.7% increase of extracted power with respect to a sequentially optimized design, highlighting the benefits of morphing and the potential of the proposed approach.
Export citation and abstract BibTeX RIS
1. Introduction
Airborne wind energy (AWE) is a comparatively young technology that aims to extract power from high altitude winds through the use of tethered airborne systems. In comparison to conventional wind turbines, these systems can reach higher altitudes, characterized by stronger and more consistent winds, and therefore potentially extract more power. Additionally, lower manufacturing and material costs are expected, due to the lack of expensive infrastructure like wind turbine towers and foundations [1]. In recent years, the research activities and commercial interest in the field of AWE increased drastically. Most studies focus on the 'crosswind power concept' first introduced by Loyd [2] in 1980. In this approach, kites or rigid wings fly crosswind trajectories, and either use the high lift forces to drive a ground based generator via a tether (lift mode), or use the high flight velocities to drive on-board wind turbines (drag mode). Both the lift and drag mode are investigated by various start-ups and academic research groups. Most academic groups work with kites, as they are generally less expensive, whereas most start-ups rely on rigid wings (Makani Power, Ampyx Power), as this technology seems more promising in terms of performance due to their favorable aerodynamic efficiency [3].
Currently, the control and automation of the airborne system is regarded as one of the major challenges, hence attracting the attention of most research groups investigating AWE systems. The majority of studies focus on developing different strategies for the control and optimization of the traction-phase flight trajectory, as well as automating both the take-off and landing of the airborne system and the transition between the different flight phases.
Next to the control and automation aspects, the structure and aerodynamics of the airborne system are crucial to extract maximum power. In terms of optimal performance, the wide range of wind speeds in which the airborne system needs to operate represents a big challenge. Additionally, the operational environment is particularly demanding due to the presence of gusts, as these have the potential of increasing significantly the load factor, hence leading to the necessity of constraining the flight envelope and possibly reducing the power production. Taking this into account, conventional rigid wings would not represent an entirely optimal solution, as their design is always the result of a compromise between the requirements of different flight conditions. Therefore, given the wide range of wind speeds at which the AWE system operates, conventional wings would mostly lead to sub-optimal performance.
Morphing structures, often referred to as 'smart', on the other hand, are characterized by their ability to adapt to different conditions. This characteristic enables to adjust specific system properties to reduce the compromise otherwise resulting by the conflicting design requirements. Morphing wings, in particular, have the potential to adapt to various flight conditions by tailoring their airfoil shape and spanwise lift distribution, therefore operating at optimal performance over the whole range of wind speeds [4, 5]. Additionally, they offer the possibility to actively alleviate gust loads by virtue of distributed, compliant shape changes, and therefore expand the flight envelope and increase the power production of the AWE system.
The major challenges of applying morphing structures to AWE wings are the high lift forces required to maximize the power output, resulting from the high flight speeds permitted by the crosswind flight path. The resulting extremely high aerodynamic forces acting on the morphing structure require the wing to be extremely stiff to withstand these loads, but still compliant enough to achieve the required shape adaptability to operate optimally across different flight conditions.
In this work, a procedure to concurrently optimize the aerodynamic shape, wing structure, and composite layup of a morphing wing for 'lift mode' AWE applications in terms of power production per wing area is presented. The optimization procedure is applied to a reference wing, with an area of approximately , operating at typical offshore wind conditions.
In the following section, the wing concept, the analysis framework, and the analytical models to assess the performance of an AWE system are presented. In sections 3 and 4, the wing optimization procedure and results are described, followed by the actuation optimization in section 5. Finally, the main findings and conclusions are summarized in section 6.
2. Wing concept and analysis framework
In this section, the aircraft configuration and the morphing wing concept is presented, followed by the description of the analysis method, the fundamental AWE analytical models, and the wind distributions typically experienced by AWE systems.
The aircraft configuration considered within this work is based on the concept presented by Makani Power [6], shown in figure 1. The tether is split in three leads, attached not only at the fuselage, but also at the wing, to increase the structural efficiency of the wing in comparison to conventional cantilever wings. This has the benefit of significantly reducing the root bending moment of the wing. In this investigation, the design of the other components of the AWE airplane (e.g. fuselage, tail empennage) is determined prior to the optimization, and frozen throughout the study. This simplification does not lead to a loss of generality, as the impact of wing parameters changes on the other components would be extremely minor. Thus, the resulting performance of the system is exclusively linked to the wing design, facilitating the process of identifying the benefits permitted by different morphing designs.
Figure 1. Aircraft configuration with three tether attachment points based on the concept of Makani Power [6].
Download figure:
Standard image High-resolution image2.1. Morphing wing concept
The morphing wing concept investigated in this study, shown in figure 2, is developed from the compliant structure introduced by Molinari et al [7–10], and attains variations of the local lift coefficient (cl) by means of chordwise morphing. Differently from the concept introduced by Molinari et al, in the proposed design the mechanical energy required to morph the structure is provided by electromechanical linear actuators instead of active piezoelectric elements. These actuators are chosen due to their higher static load-carrying capability (capacity of maintaining a fixed position without using energy), their energy density, and their favorable force-displacement characteristics [11, 12]. The deformation introduced by the actuators is guided by a numerically optimized distributed compliance rib. The actuators and ribs are organized in rib-actuator sets, consisting of a rib pair and a single actuator. To achieve the desired shape changes, the possibility to elongate part of the compliant skin is crucial, therefore, a corrugated skin with highly anisotropic stiffness is introduced on the lower side of the wing. This corrugated skin allows the desired in-plane elongation to occur, while contributing to withstand the large bending loads experienced by the structure [13–15].
Figure 2. Representation of the wing morphing concept.
Download figure:
Standard image High-resolution imageOverall, the wing consists of nine evenly distributed rib-actuator sets per half span. A stiff D-nose wing box carries the majority of the bending, shear and torsional loads. The material used for the wing and for the internal compliant rib is carbon fiber reinforced plastic (CFRP) owing to its anisotropy and favorable lightweight characteristics. The layup is concurrently optimized with the structure and aerodynamic shape, and is presented in section 3.1.
2.2. Aeroelastic analysis method
Owing to the high wing loading and to the compliance of the entire wing—and particularly of its compliant section—it is necessary to consider aeroelastic interactions to accurately predict the aerodynamic and structural behavior and to assess the resulting performance. The response of the wing on actuation inputs and aerodynamic loads is thus assessed by using a two-way weakly coupled 3D static aeroelastic analysis tool [7]. The aerodynamic behavior of the wing is simulated with a 3D panel method [16, 17] and a nonlinear extended lifting-line technique [17, 18], the latter using XFOIL [19, 20] to calculate the sectionwise 2D aerodynamic characteristics. The structural behavior is assessed by means of a 3D finite elements model. The wing skin and internal structure are modeled by plate elements, the stringers and actuators are modeled, respectively, as beam and as thermally-expanding rod elements, and the corrugated skin is modeled using flat elements and a substitute plate model [21, 22]. The aeroelastic analysis tool, validated through high fidelity numerical simulations and wind tunnel tests [7, 10], iteratively assesses the aerodynamic characteristics (lift and drag) and the structural displacements caused by actuation inputs and aerodynamic loads.
2.3. AWE performance modeling
In this study, analytical models are used to assess the energy extraction capabilities of the AWE wing. The power P produced by an AWE system in the traction phase at optimal reel-out speed (the reel-in phase is neglected in this investigation, as it is strongly dependent upon the followed trajectory) can be modeled as a function of the lift and effective drag coefficient cL and cD, the wing area , wind speed VW, and angle between tether and ground
[1, ch 1]:

The effective drag coefficient consists of the drag of the wing and also of the drag of the tether. Houska et al [23] suggest the following approximation:

At a given wind speed, the flight speed at optimal reel-out speed (
=
VW) can be calculated as [1, ch 1]:

The influence of the mass of the aircraft on the power output of the AWE system can be considered in the analysis by increasing the tether elevation angle by
(cosine losses), and by rolling the aircraft into the circular trajectory (of radius r) to counteract centrifugal forces [1, ch 3].
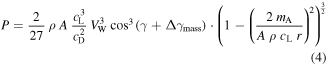
The mass of the wing is obtained from the FE model, and the mass of the fuselage is set to
, to account for the mass of the wing-to-tail connection, the tail empennage, and the electronics. The mass of the actuators is determined as a function of the required power using the relation
[11]. The required actuators power output can be calculated by the force acting on the actuator, assessed within the aeroelastic simulation, the maximum stroke of the actuator, and the maximum time required to fully activate the actuator, which is set to
.
From formulas (1)–(4), the maximum power output of an AWE wing with known aerodynamic properties (lift and drag coefficient) can be calculated as a function of the wind speed. To predict the average annual power production in the following optimization, the performance of each individual wing is assessed at four flight speeds and corresponding angles of attack, where V3 is the design flight speed, V2 and V1 are, respectively, the intermediate and the slow flight speed, and V4 is the design speed plus gust speed assuming a horizontal gust1 .

The aerodynamic coefficients (cL and cD) at the other flight speeds are determined by linear interpolation and constant extrapolation from V1 to . The power can then be assessed for flight velocities ranging from
to
. At
, the maximum tether force and wing loading
is reached. After V3 is reached, the reel-out speed is increased to limit the force acting on the wing, while still extracting power. Apart from limiting tether and wing loading, the power of an AWE system is also constrained by the nominal generator power. However, as the focus of this study lies on the wing and not on the overall system, no constraint on the maximum power is enforced. As a result, the power at velocities exceeding
is calculated by:

With this set of formulas, the average power output of the AWE system can be calculated by considering the wind distribution probability fW as:

At V4, the morphing capability at high loads is investigated. The compliant section of the wing is fully deflected upwards over the whole span and the ability to alleviate gust loads is studied. The time to fully deflect the actuator is set to , shorter than the rise time of an extreme gust [24]. The gust velocity is calculated after the IEC 61400-1 standard [25]. The detailed integration into the optimization procedure is explained in section 3.2.
2.4. Wind distribution
The wind distribution probability used in this study is the average wind distribution at the locations of all conventional offshore wind parks with a minimum capacity of at altitudes of 50, 100, and
[26, 27]. The rationale for the choice of these locations is that AWE systems placed offshore show greater potential due to the stronger and more uniform winds compared to systems located onshore. Additionally, visual and acoustic impacts of offshore systems are smaller compared to their inland counterparts [28].
The calculated average offshore wind distribution is shown in figure 3.
Figure 3. Average wind distribution at the location of offshore wind parks () at altitudes of
(continuous line),
(dashed line), and
(dotted line).
Download figure:
Standard image High-resolution image3. Wing optimization
The goal of the optimization is to identify the ideal morphing wing design, maximizing the power output of an AWE system for the aforementioned wind distribution. In this section, the optimization procedure is described. First, the parametrization of the aerodynamic shape, geometry of the internal structure, and composite layup is introduced. Thereafter, the optimization goals, constraints, variables, and initial conditions are outlined.
3.1. Parametrization
3.1.1. Aerodynamic shape
In this study, both the wing planform and its cross-sectional shape at the rib-actuator positions are optimized. The cross-sectional shape is defined by a Bezier-PARSEC parametrization BP3434, an improved Bezier parametrization relying on 15 parameters to represent a large set of airfoils, particularly well-suited for strongly cambered high lift airfoils [29, 30].
The wing planform is specified by the span and by defining the chord length and sweep at the different spanwise stations. Additionally, the twist is also defined at these locations. The planform and shape at spanwise locations between the rib-actuator sets is obtained by linear interpolation.
3.1.2. Structure
The compliant rib structure, shown schematically in figure 4, is described by a Voronoi-based parametrization [7, 31]. The main advantages of this parametrization are the small number of variables to describe the structure, its stability properties (small variable changes lead to small shape changes), and the fact that the obtained structure has no unconnected nodes and segments. In addition to the coordinates of the Voronoi-sites, the thickness of the segments is considered in the optimization, as well as the width of the rib. Having twelve Voronoi-sites, a total of 37 design variables per rib are used. The actuator is defined by four design variables per rib: three describe its position (vertical position at spar yAF, vertical and horizontal position at trailing edge yAR and xAR), and one defines the maximum stroke of the actuator. At the design flight speed, the actuators are unactuated. At both speeds and
, the actuators are activated at an optimized level (p1 and p2) ranging from −1 to 1, and at gust speed, the actuators are fully actuated at a uniform level
. Additionally, the position of the spar and the position of the corrugation is defined as a design variable (horizontal position spar xS, horizontal position corrugation xC, length corrugation
), and the position of the outer tether attachment point (TAP) can be varied along the spanwise direction.
Figure 4. Actuation (dotted line), corrugation (thin dashed line), spar (thick dashed line), and Voronoi-based internal compliant rib structure (thin continuous line).
Download figure:
Standard image High-resolution image3.1.3. Wing skin and spar layup
The wing skin and spar composite layup ply thickness is concurrently optimized with the wing structure and the aerodynamic shape. The wing skin is split in four sections along its span, and in five sections in chordwise direction, leading to a total of 20 skin-sections, shown in figure 5. The five sections in chordwise direction are the wing box, the top intermediate and top rear section, the bottom section, and the corrugation. The wing box section has a [0°, 90°, ± 45°, 90°, 0°] layup, of which the thickness of the individual CFRP Unidirectional (UD) plies are considered as design variables2 . The thickness of the composite layers of the top rear, top intermediate, and bottom segments are parametrized with two design variables, and feature a [0°, 90°, 90°, 0°] CFRP UD layup. The skin at the location of each compliant rib is reinforced with an additional 90° CFRP UD ply, resulting in one additional design variable per rib-actuator set. Likewise, the internal compliant rib structure consists of 90° CFRP UD. The corrugation layup is constant, whereas the upper and lower stringer thickness and cross-section and the spar thickness can be varied, resulting in the last five design variables.
Figure 5. Composite layup sections: wing top and bottom view.
Download figure:
Standard image High-resolution imageThis parametrization leads to a total of 604 design variables, summarized in table 1.
Table 1. Design variables.
Group | #DV | Design variables |
---|---|---|
Aerodynamic | 161 | 15 × 9 airfoil, 1 span |
shape | 9 chord, 8 sweep, 8 twist | |
Structure | 356 | 36 × 9 Voronoi, 9 corrugation |
9 rib width, 9 spar, 4 stringer | ||
1 tether attachment point | ||
Actuator | 36 | 4 × 9 actuation |
Layup | 44 | 36 skin, 4 rib, 4 spar |
General | 7 | 1 velocity, 1 tether length |
2 actuation gains (at V1 and V2) | ||
3 angles of attack (at V1, V2, V3) | ||
Total | 604 |
3.2. Optimization
In this study, parameters related to different disciplines (structure, aerodynamics) are optimized concurrently. This increases the complexity of the optimization compared to a sequential approach, but will result in the identification of a better-performing individual, due to the possibility of assessing and exploiting interdisciplinary interactions [32]. The objective of the optimization is to maximize the average annual power production per wing area of a morphing AWE system. The goal of maximizing the power per wing area instead of maximizing the overall power prevents the optimizer from simply increasing the area of the wing to improve the objective function. Increases in wing area are still beneficial, as the relative tether drag decreases with increasing wing area. The analytical models discussed in section 2.3 are used to evaluate the power output of the system.
The optimization includes two constraints. The first aims to ensure a wing design with sufficient morphing capacity, able to alleviate extreme gust loads [25]. This constraint is expressed by imposing that the lift generated when flying at gust speed with the wing fully morphed to reduce the lift has to be smaller or equal than the lift at the design speed with the actuators inactive, resulting in the constraint:

The second constraint requires the final design to withstand the aeroelastic loads without incurring buckling.

Designs satisfying this constraint were found to simultaneously fulfill strength criteria [9], hence no additional structural constraints are imposed. Dynamic aeroelastic instabilities of the wing are not investigated in the optimization, as preliminary studies showed the flutter speed of the investigated wing to be outside of the flight envelope. To confirm this, the flutter speed of the final wing has been assessed in a subsequent step, confirming the validity of the assumptions and the findings of the preliminary study3 .
The optimization problem can therefore be formulated as follows:
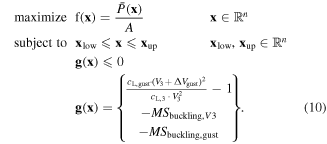
The objective function f(x) is defined as the average annual power production per wing area. The inequality constraints are related to the morphing capability at gust loads and the buckling load coefficients at V3 and
.
The optimization is performed using the algorithm covariance matrix adaptation-evolution strategy (CMA-ES) [34], previously used by Molinari et al [7], as it satisfies the requirements of being able to treat nonsmooth objective functions and of dealing with a large number of design variables.
3.3. Initial condition identification
Due to the complexity of the problem and the limitations imposed by the constraints, identifying a suitable initial guess is not trivial. To this purpose, the initial wing design is identified through two sequential pre-optimizations. First, a purely aerodynamic optimization, relying on XFOIL, is conducted to identify the initial airfoil shape of the wing. The airfoil shape, common to all wing sections, is parametrized through the Bezier-PARSEC technique previously discussed. Aeroelastic effects are neglected and the airfoil shape is optimized in terms of average annual power production per wing area using the analytical models and wind distributions defined in section 2.3. 3D aerodynamic effects are modeled through analytical approaches to predict the induced drag assuming a constant Oswald factor equal to e = 0.7. With this pre-optimization, first insights about optimal airfoil shapes for AWE wings are gathered.
A preliminary sizing for the various structural components, in order to guarantee the load-carrying capacity and perceivable morphability for the initial guess, is obtained by concurrently optimizing the initial wing structure and composite layup. This second pre-optimization uses the same analysis and optimization tools as the main optimization, however, the objective is to minimize weight whilst achieving the desired morphing capability.
The performance of the initial wing defined by these two pre-optimizations is referred to as 'optimization 0' and is included in the comparison presented in the following section.
4. Wing optimization results
To assess the impact of the various parameters on the performance of the wing, the main aerostructural optimization of the AWE system is performed three times, using increasingly wider search spaces, shown in figure 6.
Figure 6. Optimization procedure and search space for different optimizations.
Download figure:
Standard image High-resolution imageIn the first, the variables defined as 'General' in table 1 are optimized. In the second, also the 'Aerodynamic shape' variables are optimized, and in the third case, the full set of design variables is optimized.
- Optimization 1: 7 design variables
- Optimization 2: 168 design variables
- Optimization 3: 604 design variables
To compare the aerodynamic performance of the optimized wings featuring different areas, the power harvesting factor is introduced, which is defined as the ratio between the extracted power P and the theoretical wind power PA flowing through the wing area A [1].

The power harvesting factor, the weighted average power per wing area, the mass of the wing, and the design flight speed for the different optimizations are shown in figures 7 and 8. The continuous improvement of the objective function, permitted by an increased number of design variables, is a necessary—albeit not sufficient—indicator of the convergence of the optimization. Given the complexity of the optimization and the large number of design parameters, the capacity of the algorithm to converge is indeed not guaranteed. In the following paragraphs, the impact of the various design variables groups on the objective function is investigated in greater detail.
Figure 7. Objective function and power harvesting factor for different optimizations. (a) Objective function: weighted average power/area. (b) Power harvesting factor
Download figure:
Standard image High-resolution imageFigure 8. Aircraft mass and design flight speed for different optimizations. (a) Wing, actuator and fuselage mass. (b) Optimized design flight speed V3.
Download figure:
Standard image High-resolution image4.1. Optimization 1
In optimization 1, only the 'General' design variables are optimized. The main difference with respect to optimization 0 is that the wing is optimized in terms of power per area and not in terms of weight and morphing capability. Additionally, the angle of attack is optimized at each considered speed, and the wing is actuated at V1 and V2, leading to an increase in weighted average annual power production per wing area of 3%.
4.2. Optimization 2
In optimization 2, the 'General' and 'Aerodynamic shape' variables are optimized simultaneously. In figure 9, the initial and optimized wing planforms are shown. It can be seen that the planform of the wing is drastically changed. The wing chord length is increased at the root and decreased at the tip of the wing, leading to a decreased induced drag and reduced bending moment, ultimately decreasing the structural weight. The total wing area is increased from 5.1 to , decreasing the relative tether drag as previously discussed. In figure 10, the optimized airfoil geometry is shown. Compared to the initial airfoil (optimization 0 and optimization 1), identified through the pre-optimization, the airfoils at the different sections show distinctive properties, being even more strongly cambered and thick at the root (high lift, supported by inner tether), slightly less cambered and thicker around the outer TAP (high bending moment due to outer TAP), and even less cambered towards the tip (to reduce induced drag and bending moment).
Figure 9. Wing planform for different optimizations.
Download figure:
Standard image High-resolution imageFigure 10. Airfoil geometry and internal structure for different optimizations (internal structure of Opt 0, Opt 1, and Opt 2 defined in pre-optimization).
Download figure:
Standard image High-resolution imageAs a result of the optimized planform and airfoil geometry, the power harvesting factor is increased, as shown in figure 7(b), resulting in a 35% higher weighted average annual power production per wing area.
Figure 8(a) shows that the structural weight of the wing increases between optimization 1 and optimization 2, due to the larger wing area of the latter individual. The increased weight normally leads to a performance decrease. However, due to the thicker cross-sections of the wing compared to the initial design, the bending stiffness is increased and the flight envelope is enlarged. In detail, it leads to an increase in the design flight speed V3 (shown in figure 8(b)) from at the first stage of the optimization to
at the second stage, leading to the higher power production.
4.3. Optimization 3
In the last optimization, the design space is further enlarged from 168 to 604 design variables, accounting for the wing structure and composite layup, and leading to an additional improvement of the objective function by 8%. The final internal structure changes slightly with respect to the initial pre-optimized structure. The airfoil shapes are very similar to the previous optimized shapes, being slightly thicker at the root to additionally increase the bending stiffness. The layup thickness at the different sections is shown in figure 11. It can be seen that the maximum thickness is reached at the wing box of section 1. The thickness at section 2 is slightly decreased compared to section 1. At section 3, the skin needs to be reinforced due to the outer TAP, and thus the thickness increases again.
Figure 11. Composite layup thickness of optimization 3.
Download figure:
Standard image High-resolution imageThe ply thickness is optimized as a continuous design variable, possibly leading to infeasible designs. Therefore, depending on the manufacturing method and available material, the final ply thickness needs to be adjusted in a post-processing step.
5. Actuation optimization
Further improvements in the performance of the designed wing can be attained by fully exploiting the adaptability enabled by morphing. Compliant deformations, achieved by independent activation of the actuators, enable to attain wing shapes with improved aerodynamic performance for each flight condition throughout the flight envelope.
The identification of the ideal actuation strategy could be performed independently for each flight speed, requiring however a large number of optimizations. An alternative technique relies on a multi-objective optimization, capable of identifying Pareto-optimal solutions, and on specifically crafted objective functions, to identify simultaneously the ideal actuation strategy across all flight speeds [35]. In particular, the objective function aims at simultaneously minimizing the conflicting requirements, flight velocity and negative power output, of the AWE system, considering the final wing design identified in optimization 3.
The optimization problem can be formulated as follows:
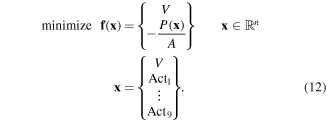
In this study, a multi-objective CMA-ES (MO-CMA-ES) [36–38] optimization technique is used due to its favorable performance compared to benchmark multi-objective optimization problems.
The analyzed individuals and the Pareto front of the multi-objective optimization are shown in figure 12 and compared with the results of optimization 3. Through this technique, the power production per wing area increases by 4.2% in average, showing the potential of the optimization method and the significance of allowing the single actuators to operate independently at each flight condition.
Figure 12. Results of the multi-objective optimization. (a) Pareto front and results of optimization 3. (b) Relative increase of power/area.
Download figure:
Standard image High-resolution image6. Conclusions
In this paper, a morphing AWE wing concept and a numerical technique to concurrently optimize the aerodynamic shape, wing structure, and composite layup of a morphing wing in terms of average annual power production per wing area is presented. The proposed morphing concept has been successfully applied on an AWE airplane with a wingspan of approximately , operating at high power harvesting factors and at velocities up to
. The optimized morphing AWE wing is sufficiently compliant to adapt its shape for the different flight situations and to actively alleviate gust loads, while being sufficiently stiff to withstands the high loads without the occurrence of static and dynamic instabilities.
The average annual power production attained by the optimized design, assuming uniform actuation of the morphing actuators, is 50.7% higher than the sequentially-optimized reference wing, mainly owing to its favorable aerodynamic shape. By optimally activating the actuators on the wing, at levels identified through a multi-objective optimization, the relative power production per wing area could be increased by additional 4.2% in average throughout the entire flight envelope. This increase greatly shows the possible benefits of applying the proposed morphing concept to an AWE wing. Minimizing the mass of the aircraft to increase the power production of the AWE system was found to play a minor role, whereas a high design flight speed and high power harvesting factor was found to be crucial, further highlighting the benefits of a multidisciplinary optimization.
The ability to actively alleviate extreme gust loads, defined by an increased flight speed of approximately at the design flight speed of
after IEC 61400-1 standard [25], leads to a 14% external load reduction, and especially demands lower control requirements on the ground station reeling system, as the effects of possible disturbances can be mitigated directly by morphing the wing.
The adaptivity of the proposed concept leads to a high versatility for the entire morphing AWE system. Furthermore, owing to the additional degrees of freedom offered by compliant shape changes, the wings become truly multifunctional devices: in addition to their load-carrying capacity with low structural mass—virtue of the lightweight structural design employed—the aerodynamically efficient shape adaptivity permits not only to optimally operate at different wind speeds and to limit the structural overload caused by gusts, but also to replace conventional control surfaces. The possibility of performing maneuvers, while maintaining the ideal aerodynamic conditions for energy extraction, can thus be exploited to follow optimized trajectories, further increasing the power harvesting capabilities of the system.
Footnotes
- 1
A horizontal gust is considered as the resulting load increment is larger than that resulting from a vertical gust. This is a result of the operating regime of AWE systems, close to the stall condition, in which an increment in incidence would lead to minor variations in lift.
- 2
The 0° layer direction is defined in spanwise direction.
- 3